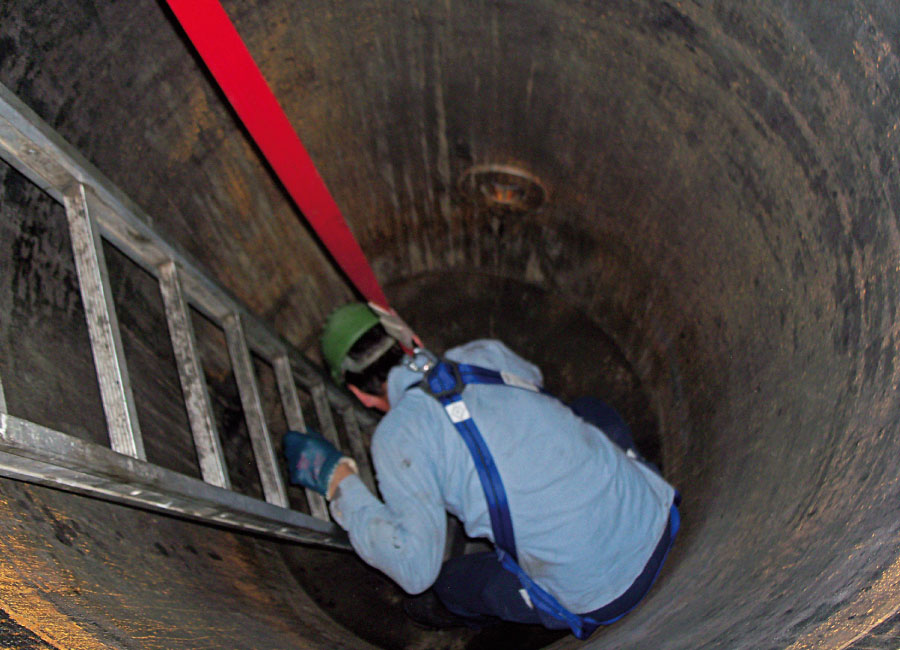
Un intervento si sofferma sullo sviluppo di un metodo quantitativo per la valutazione dei rischi nelle operazioni in spazi confinati nell’industria di processo. La normativa, il caso studio e l’implementazione di metriche quantitative per la valutazione.
Come ricordato nei nostri articoli e come mostrato dai tanti incidenti presentati nella rubrica “ Imparare dagli errori”, continuano a verificarsi ogni anno infortuni, gravi e mortali, negli spazi confinati e/o ambienti sospetti di inquinamento e spesso a causa anche di una valutazione del rischio inefficace.
Un settore che è stato particolarmente colpito da questi eventi è stato “quello dell’industria alimentare e dei bioprocessi, con infortuni a seguito di asfissia, annegamento e contatto con solventi o altre sostanze tossiche”. Questi infortuni sono “per lo più riconducibili alle attività svolte dagli operatori nello svolgimento delle operazioni di montaggio, manutenzione, pulizia, riparazione delle apparecchiature di impianto”.
A ricordarlo è un intervento che si è tenuto al convegno SAFAP “ Sicurezza e affidabilità delle attrezzature a pressione” (online, 16-18 novembre 2021) che ricorda come “un processo critico per l’industria alimentare è rappresentato dalla raffinazione dell’olio vegetale grezzo, derivato da processi di estrazione”. Ed è stata condotta una analisi degli aspetti di sicurezza relativi a “ciascuna sezione del processo di raffinazione degli olii vegetali, come la neutralizzazione, il ‘bleaching’, la filtrazione, e la deodorazione; operazioni che si svolgono in prevalenza in apparecchi sottovuoto”.
E in relazione ai residui di solvente nei serbatoi di stoccaggio e nel processo sono avvenuti in passato vari incidenti in Italia e Spagna e questo dimostra la “necessità di sviluppare un approccio sistematico a supporto della valutazione dei pericoli e dei rischi in questo tipo di apparecchiature e, più in generale, per la valutazione della sicurezza delle operazioni in spazi confinati”.
L’intervento “Operazioni in spazi confinati nell’industria di processo: sviluppo di un metodo quantitativo per la valutazione dei rischi”, a cura di G. Landucci e C. Nicolella (Dipartimento di Ingegneria Civile e Industriale, Università di Pisa), L. Ricciardi, C. Console, F. Cassandra e L. Di Donato (Inail – Dit), presenta un nuovo approccio “a supporto della valutazione dei pericoli e dei rischi per operazioni in spazi confinati e/o ambienti sospetti di inquinamento, con particolare riferimento all’industria alimentare”. E rispetto agli approcci convenzionali, viene proposta “una valutazione di tipo quantitativo”.
Nel presentare l’intervento ci soffermiamo in particolare sui seguenti argomenti:
- Le operazioni negli spazi confinati e la normativa italiana
- L’implementazione di metriche quantitative per la valutazione
- Il caso studio nell’industria alimentare e la valutazione dei rischi
Le operazioni negli spazi confinati e la normativa italiana
Nell’intervento si ricorda che la normativa italiana di riferimento – DPR 14 settembre 2011, n.177 – prescrive che “qualsiasi attività lavorativa in spazi confinati e/o in ambienti sospetti di inquinamento possa essere svolta solo da aziende qualificate o lavoratori autonomi che soddisfino i seguenti requisiti:
- piena applicazione delle vigenti disposizioni in materia di valutazione dei rischi, monitoraggio sanitario e misure di gestione dell’emergenza per le imprese;
- presenza di personale con esperienza lavorativa di almeno tre anni in spazi confinati e/o in ambienti sospetti di inquinamento;
- aver svolto attività di informazione e formazione per tutto il personale, compreso il datore di lavoro impiegato per lavori in ambienti di sospetto o confinato inquinamento, specificamente finalizzate alla comprensione dei fattori di rischio tipici di tali attività e previa verifica dell’apprendimento;
- possesso di dispositivi di protezione individuale, strumentazione e attrezzature di lavoro idonei alla prevenzione dei rischi connessi all’operare in spazi confinati con o senza inquinamento ed aver svolto attività di formazione al corretto utilizzo di tali dispositivi, strumentazioni ed attrezzature”.
E per la valutazione e gestione dei rischi per i lavoratori che operano in ambienti confinati e/o sospetti di inquinamento, “è necessario tenere conto della normativa, a supporto e integrazione della quale intervengono linee guida, buone prassi e metodi quantitativi per l‘identificazione e la valutazione dei rischi”, come mostrato nell’intervento, che “possono guidare il datore di lavoro nella scelta di procedure di lavoro e di emergenza, DPI e strumenti di rilevazione dei parametri ambientali”.
L’implementazione di metriche quantitative per la valutazione
Veniamo alla metodologia vera e propria riassunta nella figura che riprendiamo dall’intervento:
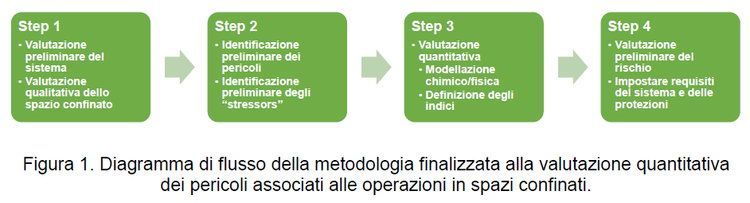
La prima fase (step 1) è, dunque, “finalizzata ad una caratterizzazione preliminare del sistema in analisi e del suo funzionamento. Questa fase è qualitativa e offre valutazioni cruciali, in quanto identificare la presenza di un’operazione in spazi confinati è uno screening complesso e influisce sui passaggi successivi”. Successivamente, “viene eseguita la valutazione preliminare dei pericoli potenziali” (step 2), supportando “la definizione di fattori di stress rilevanti per il sistema e il funzionamento”.
Si indica che i fattori di stress sono “qui considerati come tutti gli agenti chimici, fisici o biologici rilevanti che causano una risposta avversa sull’operatore. Particolare enfasi è data agli inquinanti, alle sostanze tossiche e infiammabili, in quanto il metodo è dedicato all’industria di processo, dove vengono lavorate e stoccate sostanze pericolose. Tuttavia, l’approccio è adatto a diversi tipi di fattori di stress, come rumore, vibrazioni, shock elettrico, ecc., e può essere esteso ad altri settori industriali”.
Dopo l’identificazione dei fattori di stress rilevanti per il sistema, “si definiscono i relativi parametri quantitativi, finalizzati alla valutazione complessiva dello stato del sistema”. E nello step 3 questi parametri “sono dapprima modellati attraverso relazioni chimico/fisiche di tipo deterministico. Ciò consente a chi effettua la valutazione del rischio di avere un quadro in tempo reale dello stato del sistema, evidenziando potenziali pericoli legati alle sostanze tossiche e/o infiammabili potenzialmente presenti in una o più operazioni nello spazio confinato identificato nello step 1. Per supportare la valutazione del livello di rischio, vengono introdotti indici specifici derivati dai risultati modello deterministico”.
Infine, lo step 4 consiste in “una valutazione del rischio delle operazioni in spazi confinati, basata sulle informazioni quantitative ottenute nelle ultime fasi. In tale fase, possono essere anche definiti i requisiti funzionali per l’operazione, il livello e tipologia di addestramento degli operatori e le eventuali protezioni individuali”.
Il caso studio nell’industria alimentare e la valutazione dei rischi
L’intervento presenta l’applicazione di questo metodo al settore della raffinazione dell’olio vegetale, con la descrizione delle operazioni, l’identificazione dei fattori di stress, la definizione del caso studio, l’impostazione della simulazione di processo e la definizione degli indici di pericolo.
Sono poi mostrati i risultati ottenuti per le operazioni nei serbatoi di stoccaggio e riprendiamo, dall’intervento, una figura che mostra i risultati ottenuti nella valutazione del caso studio, riportando il valore numerico dell’indice di hazard level (rappresentato da linee verticali scure nell’istogramma) e la relativa classificazione di pericolosità. Si ricorda che il valore dell’indice di pericolosità per l’operazione in spazio confinato (CSI) “cambia in base sia alle condizioni di stoccaggio che a quelle ambientali. I risultati ottenuti portano alla valutazione dei periodi più critici per le operazioni di ingresso, in particolare per il mese di giugno quando CSI = 4 per più giorni, a causa dell’elevata temperatura ambiente e il tenore di esano residuo considerato. Un valore così alto di CSI può indicare condizioni pericolose nel serbatoio, sia per gli operatori che per l’integrità stessa dell’apparecchio, poiché l’innesco accidentale dell’atmosfera esplosiva può portare a gravi danni alle apparecchiature e alle unità vicine”.
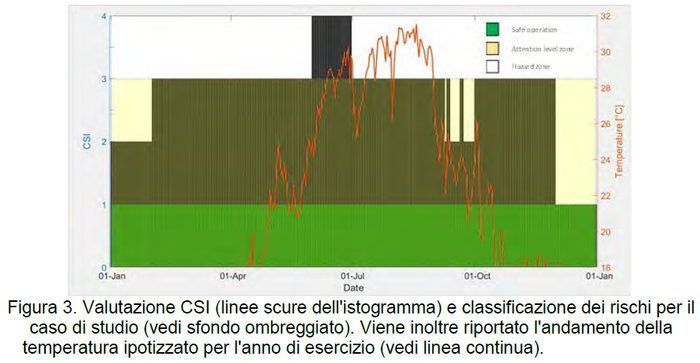
Sulla base del CSI calcolato secondo la presente metodologia, “la valutazione del rischio delle operazioni di manutenzione può essere supportata da informazioni in tempo reale derivate da modelli chimico/fisici. Queste informazioni possono essere integrate nelle procedure convenzionali per l’analisi della sicurezza sul lavoro, supportando la stima del rischio per l’operazione in questione. Allo stesso tempo, possono essere derivati i requisiti funzionali per migliorare la sicurezza delle operazioni in stabilimento. Nel caso di operazioni di accesso in serbatoi di olio vegetale greggio, è stata riconosciuta di fondamentale importanza l’adozione dell’uso sistematico di inertizzazione tramite azoto o di vapore prima delle operazioni e/o di specifiche procedure di accesso (drenaggio completo delle apparecchiature, ventilazione ecc.) soprattutto per alti valori di CSI”.
Dunque il lavoro mostrato nell’intervento ha avuto l’obiettivo di “sviluppare una metodologia per la valutazione dei pericoli e dei rischi in ambienti di lavoro confinati e/o sospetti di inquinamento”. E rispetto agli approcci convenzionali adottati per le analisi della sicurezza sul lavoro, si mostra come “i parametri fisico/chimici relativi sia all’attività lavorativa che all’ambiente possono essere entrambi convertiti in metriche rigorose a supporto dell’identificazione preliminare dei pericoli. La novità introdotta dal metodo è relativa all’implementazione di un approccio termodinamico rigoroso, basato su relazioni chimico/fisiche e simulazione di processo, che consente l’analisi quantitativa del sistema. Pertanto, informazioni importanti possono essere ricavate per supportare successive valutazione dei rischi e per l’implementazione di procedure di lavoro e di appositi percorsi di formazione e addestramento degli operatori”.
Si conclude segnalando che viene preso in considerazione l’esempio dell’industria alimentare e della raffinazione dell’olio vegetale, ma il metodo “è adatto all’estensione in qualsiasi campo caratterizzato dalla presenza di sostanze pericolose con conseguenti pericoli tossici e/o infiammabili per gli operatori. La possibilità di sintonizzare l’approccio su qualsiasi settore origina un potente strumento da implementare nel sistema di gestione operativo della sicurezza”. Si ricorda, infine, che il metodo applicato in questo lavoro “è in una fase preliminare di sviluppo ed è adatto a fornire informazioni generali sulle varie tipologie di incidenti in ambienti di lavoro confinati e/o sospetti di inquinamento”. E – concludono gli autori – “il coinvolgimento delle associazioni di categoria per la mappatura degli incidenti nell’industria alimentare, con particolare riferimento alla produzione di vino e olio d’oliva, è un passaggio cruciale per lo sviluppo di buone prassi e per supportare le attività di aggiornamento della normativa di settore”.
Rimandiamo, infine, alla lettura integrale dell’intervento che riporta molti altri dettagli e informazioni anche in relazione al caso studio affrontato.
Scarica il documento da cui è tratto l’articolo:
Inail, Dipartimento innovazioni tecnologiche e sicurezza degli impianti, prodotti e insediamenti antropici, “ SAFAP 2021 – Sicurezza e affidabilità delle attrezzature a pressione”, atti del convegno SAFAP 2021, editing di Francesca Ceruti e Daniela Gaetana Cogliani, edizione 2021
Fonti: Puntosicuro.it, Inail